In my roles as a designer, I have taken a technical hands-on approach to developing the methods of production through processes, fixtures, tooling and even custom built machines.
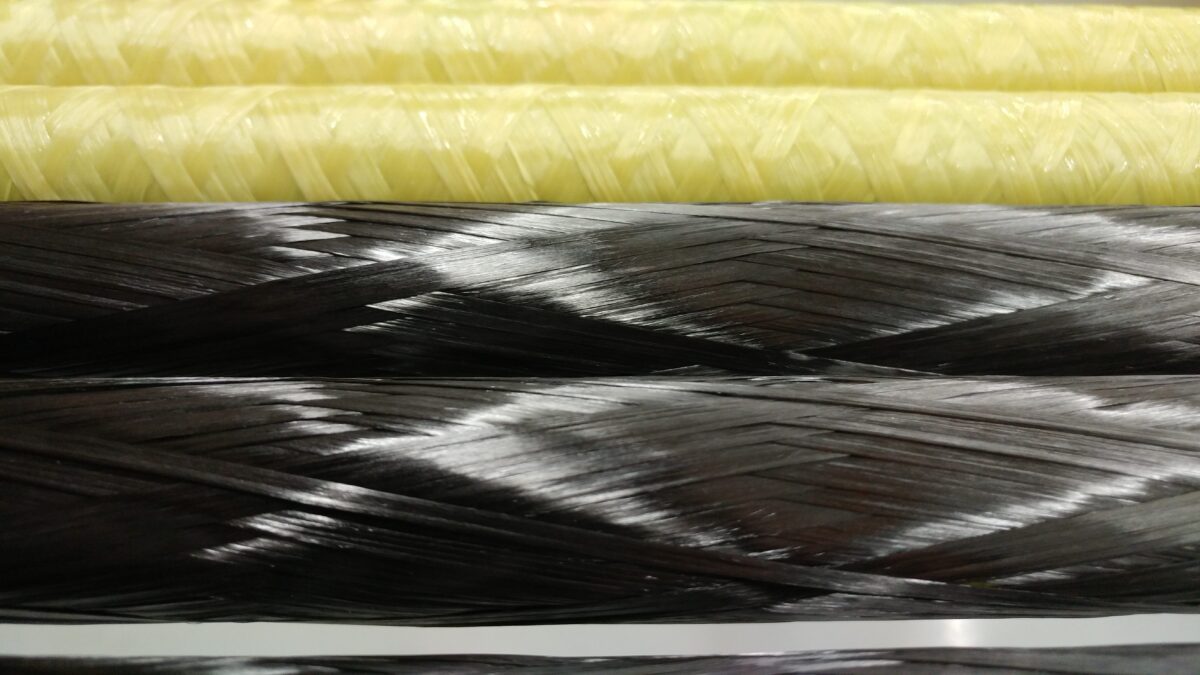
Composite Production Machinery
To produce composite parts, such as the above picture, requires a discrete layup of two or more materials with specific orientations and chemical/ mechanical properties to be bonded by resin.
Typically to bond the layers well and homogeneously without air bubbles, pressure and high heat is used to cure the parts.
Working closely with the chief engineer at Paterson Composites, I developed various production methods and designed parts to improve production. From aluminum and steel components, to personally glued-up carbon assemblies such as the Layup Head, pictured below, we progressively innovated to hit our production goals.
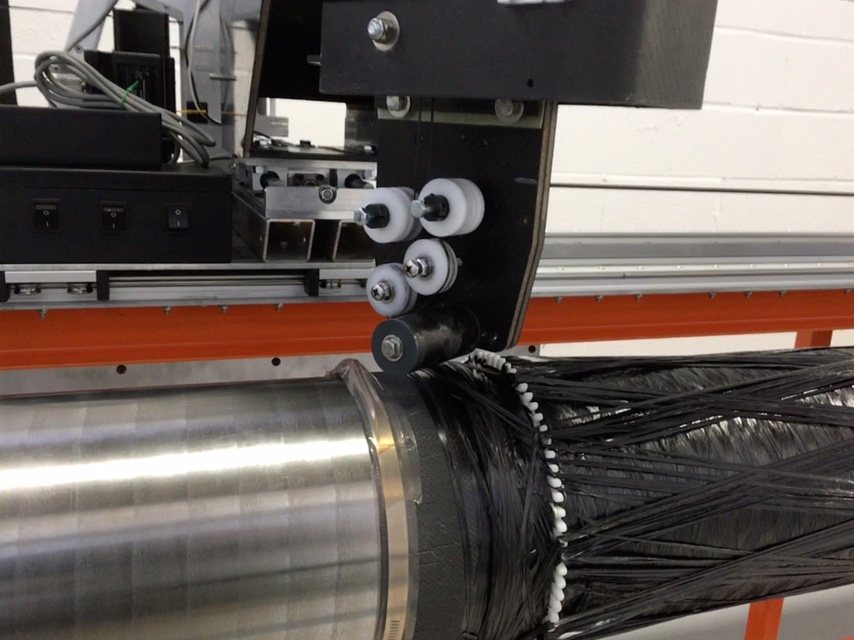
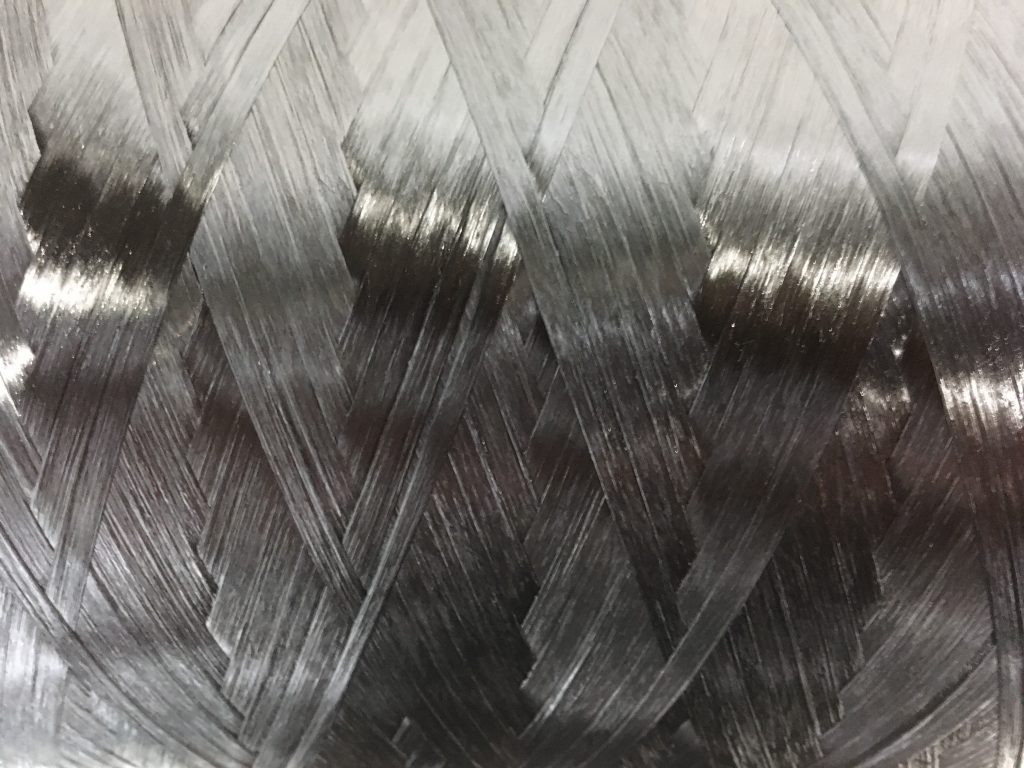
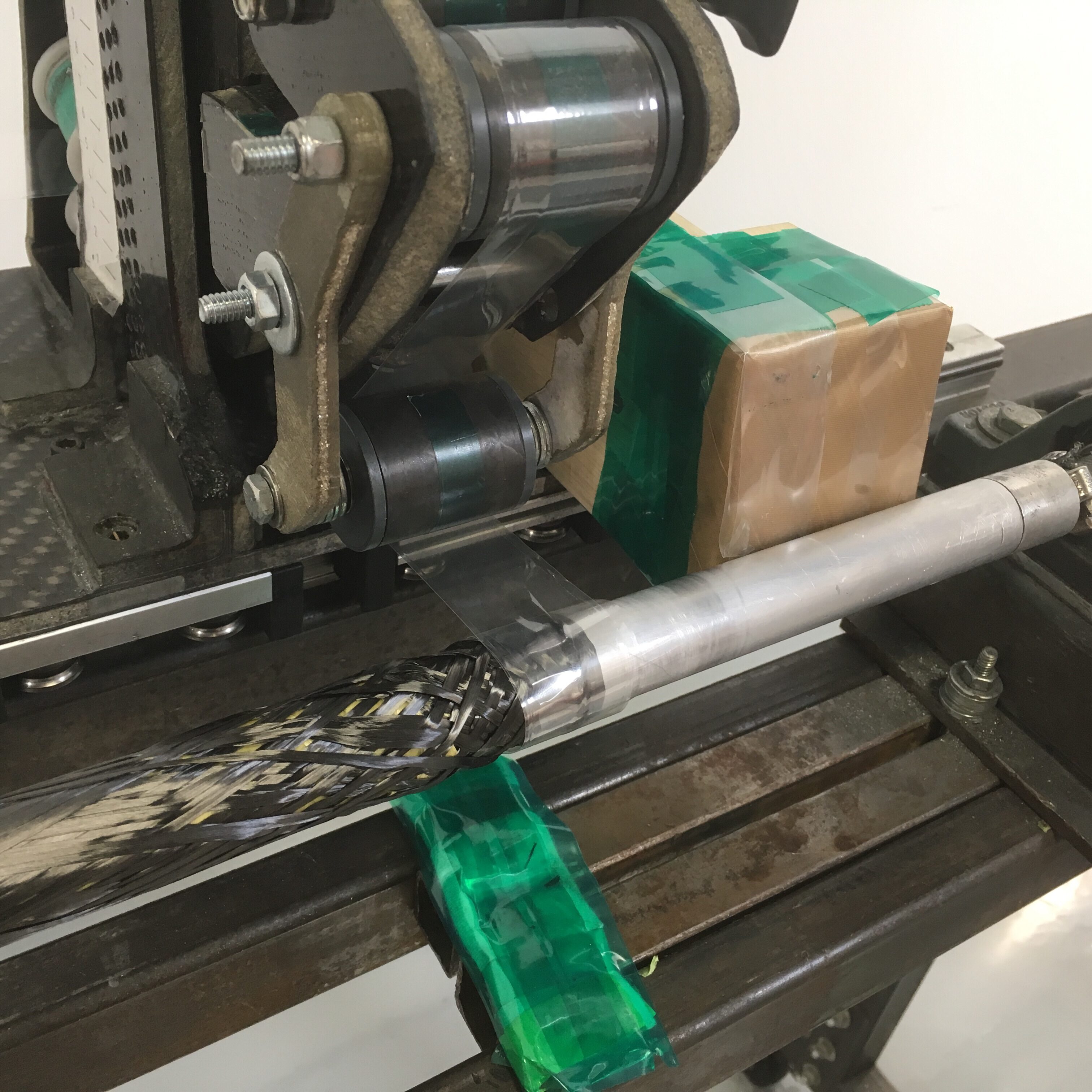
For tubes, after the filament is wound onto mandrels heat shrink tape is tightly wrapped under specific tension loads. Loaded into custom built proprietary ovens [not pictured] for a number of hours, the heat ramps up by computer control and the tape shrinks uniformly and applies a great pressure to the composite parts, squeezing excess resin from the finished piece. This is similar to method used on the Odysseus Project.
As this 24ft winder was designed and built in-house, I have some parts further documented here:
This pulley assembly is one of 4, and allows combined application of 4 composite filaments in one pass by the Layup Head.
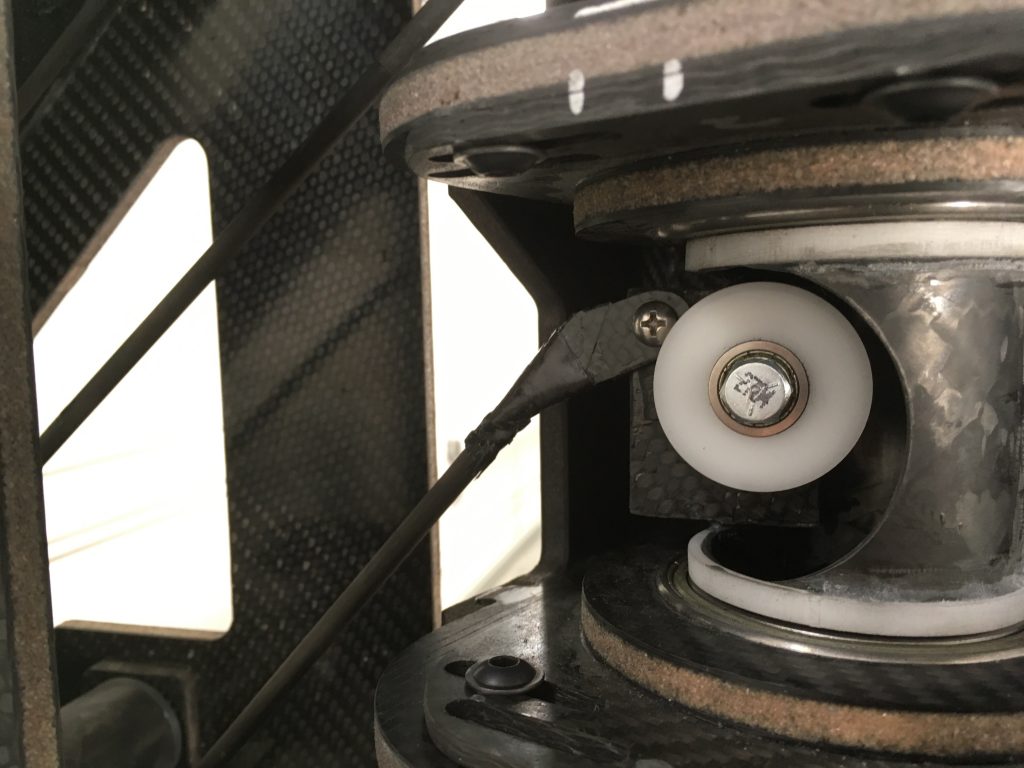
In this video you can see the main spindle’s planetary reduction gearbox spin. The gearbox is mated with an industrial servo motor with encoders for precise radial movement control.
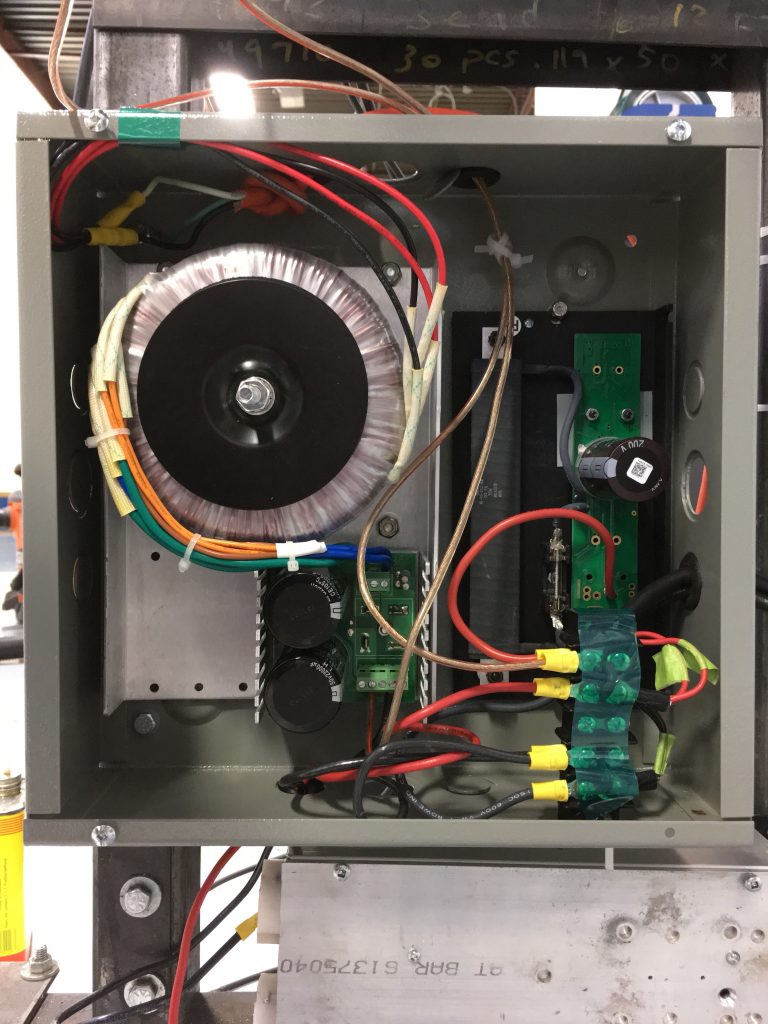
You must be logged in to post a comment.